La sostenibilità e l’attenzione al risparmio energetico sono i settori chiave sui cui le aziende oggigiorno hanno deciso di investire. Mauro Parrini e Claudio Cingolani, rispettivamente coo (chief operating officier) e head of R&D and technical department di Simonelli Group, ci hanno raccontato i passi che l’azienda ha mosso in favore dell’impatto ambientale e della sostenibilità per una filiera più green, sostenibile e produttiva. Leggiamo di seguito i loro pensieri.
Mauro Parrini, chief operating officier di Simonelli Group
Sostenibilità e risparmio energetico anche per il settore delle macchine per il caffè e le apparecchiature da bar sono temi caldi ma per Simonelli Grup sono all’ordine del giorno dal 2011 almeno da quando avete avviato il progetto Lca. Ci racconta un po’ la storia e il progresso?
“La nostra azienda è lontana dal polo industriale delle macchine per caffè espresso, per questo motivo sin dagli anni Settanta abbiamo attivato un network locale composto da centri di ricerca, università, fornitori e partner con i quali abbiamo avviato insieme un progetto di crescita sostenibile, che ci ha portato anche a cogliere importanti sfide globali come quello del climate change.
Siamo stati, infatti, tra i primi a introdurre la Life Cycle Assestment, una metodologia strutturata e standardizzata sull’analisi del ciclo vitale di un prodotto che quantifica eventuali impatti sull’ambiente.
Tutte le nostre novità vengono analizzate in questo modo da più di un decennio in collaborazione con l’Università Politecnica delle Marche con la quale cerchiamo di capire come ottimizzare in termini di sostenibilità e circolarità le nostre macchine: la carbon footprint – cioè quantità di anidride carbonica che viene prodotta dal momento di estrazione della materia prima sino alla dismissione della macchina a fine vita – è una delle linee guida che adottiamo quando creiamo nuove tecnologie e nuovi prodotti.
In particolare questa metodologia ha dimostrato come l’anidride carbonica generata da una macchina da caffè deriva per il 3/5% dalla produzione componenti e assemblaggio e per il 95/97% dall’energia consumata durante la sua attività nel coffee shop.
Abbiamo quindi iniziato a lavorare su due fronti: da un lato abbiamo studiato tecnologie e individuato nuovi materiali in grado di ridurre i consumi energetici nella fase d’uso della macchina nel coffee shop; dall’altro, ragionando a lungo termine in vista di una futura autoproduzione dell’energia da fonti rinnovabili, abbiamo iniziato a studiare nuovi materiali sempre più sostenibili e performanti.
È per questo motivo che riteniamo che i progetti sulla sostenibilità devono esser svolti in maniera scientifica. Noi lo facciamo con il nostro Centro di ricerche, collaborando con Università e laboratori, partendo dal nostro Research and Innovation Coffee Hub: analizziamo ciò che esiste negli altri mercati, ci poniamo tante domande e troviamo risposte per rispondere ai bisogni di oggi e anticipare gli scenari futuri.”
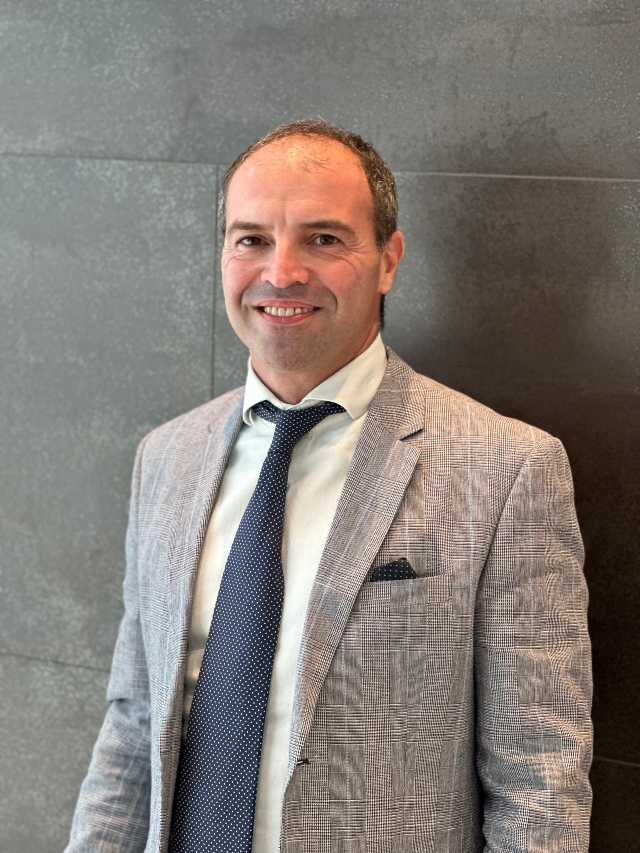
Sull’LCA, l’analisi del ciclo di vita, state lavorando da tempo: di quanto è stato ridotto l’impatto ambientale dei componenti e in particolare su quali componenti siete intervenuti?
“Lo studio dell’LCA è stato davvero utile per intervenire su alcuni componenti, ma soprattutto per generare nuove sfide che, ovviamente, abbiamo colto. La caldaia di Appia Life, ad esempio, è coibentata utilizzando tecnologie di isolamento all’avanguardia in grado di ridurre il consumo di energia del 13% rispetto ad Appia II.
Inoltre gli studi di Life Cycle Assessment hanno dimostrato una riduzione delle emissioni di CO2 rispetto a Appia II del 20%. Appia Life ha ottenuto questi importanti risultati grazie al nuovo sistema termico, ai nuovi materiali utilizzati e all’ottimizzazione generale delle componenti meccaniche.
Con Aurelia Wave UX abbiamo lavorato in un modo diverso, studiando una tecnologia più semplice da utilizzare e allo stesso tempo più performante. La tecnologia ITS, infatti, è il risultato della continua ricerca volta ad avere ottime performance estrattive, aumentando ancora di più la semplicità di utilizzo e il risparmio energetico. Gli studi LCA hanno di nuovo confermato la riduzione delle emissioni di Co2 del 7% rispetto al modello precedente pur mantenendo gli stessi livelli di performance, qualità del servizio e versatilità.”
La sensibilità all’impatto ambientale e al risparmio energetico in Simonelli Group esistono da tempi non sospetti. Come è nata questa sensibilità? Come ci siete arrivati ai tempi quando nessuno ne parlava? Una sensibilità innata? I vostri stretti contatti con le Università?
“Come detto prima, questa sensibilità, se così vogliamo chiamarla, nasce dello spirito innovativo dell’azienda che ha voluto costruire un network eterogeneo di stakeholders che condividono gli stessi valori e con l’obiettivo di crescere insieme e di contribuire a uno sviluppo sostenibile intercettando in anticipo le esigenze del mercato di riferimento e non solo.”
Sostenibilità dei materiali utilizzati per costruire i nuovi modelli: anche su questo aspetto si può lavorare per trovare soluzioni che durino nel tempo e che abbiano un minor impatto ambientale?
“Assolutamente sì, infatti abbiamo partecipato alla piattaforma MARLIC della Regione Marche e in particolare al progetto “De-Manufacturing” che raccoglie l’ardua sfida del recupero e del riutilizzo dei materiali compositi, andando così a rispondere ad un’esigenza forte: quella di orientarsi verso il miglioramento della sostenibilità ambientale, con importanti ricadute in termini tecnologici, economici e sociali.
Abbiamo voluto accettare una sfida importante: quella del riutilizzo di materiali compositi, estremamente difficili da riciclare, per ottenere nuovo materiale con performance e qualità superiori rispetto a quello di partenza.
Un aspetto non banale, perché spesso quando si parla di materiale riciclato, si pensa erroneamente a un risultato di poco costo e di scarso livello, mentre invece è l’esatto contrario. In collaborazione con l’azienda capofila Delta srl abbiamo definito un processo e delle tecnologie in grado di riutilizzare il materiale composito di lavorazione della stessa Delta per la carenatura della macchina da caffè Eagle One di Victoria Arduino con prestazioni di durezza, igiene (è antibatterica), lunga durata e resistenza agli urti.
Lo ritengo un esempio concreto ed efficace di simbiosi industriale in cui, del materiale frutto della produzione di un’azienda, non chiude il suo ciclo di vita divenendo rifiuto (perché difficilmente riciclabile), ma si inserisce nuovamente nel ciclo produttivo, diventando risorsa, materia prima con caratteristiche e performance superiori rispetto al materiale di partenza, per la produzione di un’altra azienda.
Una sinergia quella tra le due aziende del territorio marchigiano, che risponde pienamente ai principi tracciati dall’esigenza della transizione verso un tipo di economia circolare.”
Ci sono altre attività in questa direzione del riutilizzo?
“Il progetto De-Manufacturing si inserisce in un quadro più ampio, che vedrà lo studio e la realizzazione di un impianto di macinazione del materiale composito, necessario per il passaggio dalla fase di ricerca a quella di industrializzazione. Ovviamente questo è solo uno dei tanti progetti che stiamo portando avanti.”
Simonelli Group ha attorno a sé un gran numero di produttori di componenti, la valle del Chienti è una sorta di coffee Valley. Questo ecosistema industriale, queste collaborazioni, vi hanno aiutato nei vostri progetti di risparmio energetico?
“Si, tutti questi progetti di innovazione sul lato sostenibilità si inquadrano all’interno di una cornice più ampia che Simonelli Group si è sempre impegnata a rispettare. È la nostra filosofia. Noi siamo chiamati a portare avanti ciò che è stato creato dai fondatori di Nuova Simonelli prima e Simonelli Group poi, senza fermarsi alle cose semplici, che sanno fare tutti.
Ci interessa invece cercare delle possibili soluzioni ragionando al di là del prodotto e del contesto, partendo anche da una contaminazione tra vari settori per migliorare le performance e sostenibilità delle nostre macchine. Su questo ci sentiamo in dovere di portare avanti questo percorso di innovazione e crescita sostenibile, molto apprezzato dal mercato.”
La sensibilità dei vostri clienti, dei baristi e dei loro clienti verso il tema sostenibilità energetica è cambiata, c’è un’esigenza sentita su questo tema, in Italia e/o all’estero? Sono tante le richieste che spingono l’azienda a fare ricerca e sviluppo su questo campo?
La sensibilità dei partner, distributori, catene, torrefattori e baristi era molto alta già prima dell’attuale crisi energetica. Da parte nostra c’è la continua ricerca verso soluzioni sempre più sostenibili sia dal punto di vista ambientale che economico.
Claudio Cingolani, head of R&D and technical department di Simonelli Group
Adesso su che cosa siete all’opera?
“Ormai sono anni che ci impegniamo sul piano del risparmio energetico, realizzando sistemi di coibentazione sempre più performanti che possano conservare il calore all’interno delle caldaie, riducendo la dispersione al massimo e di conseguenza i costi energetici.
È un processo che abbiamo avviato da diverso tempo e che affiniamo continuamente, così come succede alla tecnologia che ci permette di avere a disposizione materiali sempre più efficienti in grado di portare a risultati ridotti in termini di consumo energetico.
Ancora su questo fronte stiamo facendo ricerca sull’uso di materiali più sostenibili per la realizzazione della macchina, dal telaio alla carena, sino al packaging: stiamo scegliendo soluzioni che abbiano un basso impatto ambientale.”
La macchina per l’espresso è energivora: che cosa avete studiato per far risparmiare i baristi sulla bolletta?
“Abbiamo, e già in passato, messo a punto delle tecnologie già presenti nei nostri modelli attualmente in commercio, focalizzandoci proprio sul recupero dell’energia che per esempio viene impiegata per erogare il caffè e che potrebbe esser in parte recuperata.
In questo ci siamo ispirati anche al settore automobilistico e alle macchine da corsa che riutilizzano in frenata l’energia e abbiamo quindi applicato da qualche anno un brevetto T.E.R.S (Termal Energy Recovery System) che ha vinto diversi premi, che recupera il calore dell’acqua di scarico dalle elettrovalvole dopo aver preparato il caffè, per andare a scaldare l’acqua che entra nella macchina, risparmiando fino all’8% di energia.
Si tratta di acqua a 90 gradi che normalmente la macchina getta nello scarico. Tramite un particolare scambiatore riusciamo invece a recuperare parte di questa energia per pre-riscaldare l’acqua e inserirla nella caldaia ad una temperatura più elevata.
Così si è in grado di risparmiare energia, perché il salto termico che la resistenza deve applicare sull’acqua è minore e così si riduce la bolletta elettrica.
Un’altra delle tecnologie in grado di ridurre i consumi e già presente nelle nostre macchine consiste in un’evoluzione energetica del nostro sistema multiboiler, ovvero Neo, lanciato con la Eagle One di Victoria Arduino.
NEO è un sistema di riscaldamento istantaneo dell’acqua per fare il caffè ed è separato dalla caldaia del vapore.
Sono state ottimizzate le dimensioni del boiler dell’acqua e della potenza della caldaia, in modo da ridurre al massimo la quantità di liquido che resta caldo quando la macchina non viene utilizzata, così da ridurre ancora una volta il calore disperso o che è mantenuto inutilmente all’interno dell’attrezzatura.
Vent’anni fa si lavorava con macchine molto grandi dotate di caldaie piuttosto ampie, per poter mantenere a lungo e stabili queste temperature dell’acqua. Oggi studiamo per ottenere macchine rapide, che riscaldano velocemente e che non conservano l’acqua calda troppo a lungo: questo ci permette di risparmiare energia senza sprecarla e utilizzarla solo per estrarre il caffè.
Ultimo punto, è quello inserito nella Black Eagle Maverick: abbiamo recuperato parte del calore che viene prodotto dal motore della pompa, e così l’energia che solitamente si disperde in calore viene riutilizzata per riscaldare l’acqua prima che arrivi nel ciclo idraulico della macchina, con qualche grado in più per recuperare il gap che i sistemi di riscaldamento devono offrire per raggiungere temperature desiderate. Grazie alle tecnologie T3 Genius, T.E.R.S. e il recupero dell’energia del motore della pompa abbiamo ridotto del 37% il consumo energetico della Black Eagle Maverick rispetto al modello precedente.”
Capitolo nuove tecnologie applicate alle macchine e risparmio energetico: come interagiscono?
“Ormai la digitalizzazione sta sempre più prendendo piede nelle macchine: è vero che la parte idraulica ci aiuta a recuperare il calore perso, ma anche un software evoluto insieme agli algoritmi che apprendono l’utilizzo della macchina e riescono a interagire con il barista, permettono di regolare il consumo della macchina e così ridurre gli sprechi energetici quando l’operatore non utilizza l’attrezzatura. Lo strumento impara dal barista il suo modo di lavorare, registrando i picchi di maggior flusso durante la giornata e regolando in base a questo le regolazioni delle temperature. Su questo punto studieremo sempre di più: l’elettronica ci viene in supporto per migliorare le performance e anche il consumo energetico.”
Tutto questo risparmio energetico non influisce sulla performance
“Al contrario: aiuta la macchina a funzionare meglio. Le performance non vanno a discapito del risparmio energetico e viceversa. È anche grazie all’elettronica che si possono conservare le alte funzionalità e allo stesso tempo limitare i consumi. Riusciamo a fornire delle prestazioni più elevate anche su macchine di fascia più bassa, senza penalizzare il risparmio energetico.”
Oggi il 98% dell’impronta energetica di una macchina deriva dall’uso nei coffee shop: a quanto potrà scendere?
“Parlando di numeri e riallacciandomi alle tre principali innovazioni che abbiamo sviluppato, possiamo affermare che con le nuove tecnologie come NEO e con i nuovi sistemi di coibentazione, abbiamo eliminato quasi il 35% del consumo energetico rispetto al modello precedente: questo rappresenta un taglio considerevole dei consumi energetici, considerando una giornata tipo di un coffeeshop prendendo come riferimento sia il modello italiano, dove si consuma maggiormente caffè, sia quello internazionale, dato che all’estero vengono richieste più bevande a base di latte, consumando più vapore.
Siamo in grado così di risparmiare l’8% di energia sul totale della giornata grazie al TERS, mentre il motore raffreddato, con il recupero del calore da questo generato, ci permette di scendere al 6% sull’erogazione.”
Domanda forse un po’ drastica: si potrà mai eliminare il serbatoio dell’acqua calda e scaldare il liquido direttamente sulle teste dei gruppi, magari con un sistema nuovo come l’induzione?
“Si discute molto dei nuovi sistemi di riscaldamento tra cui l’induzione. Alla domanda se si potrà mai eliminare la caldaia, rispondo che sicuramente è un obiettivo che tanti si stanno dando e ci stiamo lavorando anche noi con lo sviluppo di diverse tecnologie. Il fine è quello di riuscire a riscaldare l’acqua solo quando e dove serve. Una volta eliminato la caldaia inoltre, avremmo una libertà tecnologica maggiore: senza, si potrà modificare anche il layout classico della macchina.”
Come si può risolvere il problema del consumo energetico dovuto al grande uso del vapore che soprattutto all’estero è fondamentale
“Il concetto del vapore sicuramente si articola su due le linee: ottimizzare il rapporto tra il litraggio della caldaia e la potenza della resistenza che produce vapore; studiare poi tutti i metodi che ci permettono di generare vapore nel minor tempo possibile.”
La Aurelia è stata la prima macchina in cui avete apportato la nostra filosofia costruttiva e progettuale sostenibile. Ci può raccontare il suo percorso di venti anni di produzione verso la riduzione dei consumi?
“Siamo arrivati alla terza edizione dell’Aurelia, l’ultima nata è la Wave. Oltre a un aggiornamento estetico, tanto è stato fatto anche a livello tecnologico. Il nome ormai è iconico: per noi è stata la prima macchina che ci ha permesso di sponsorizzare il Campionato del mondo baristi, e questo grazie anche a una tecnologia dello scambio di calore che ci ha consentito comunque di rientrare nei parametri restrittivi delle gare mondiale.
In seguito ci siamo evoluti con il sistema T3 nell’Aurelia 2 e infine nella Wave abbiamo introdotto una tecnologia più semplice e alla portata di tutti, la UX, con un consumo e dei costi ridotti e performance alla pari dei modelli precedenti.”